Innovations in Injection Moulding: 3D Printing and Industry Trends
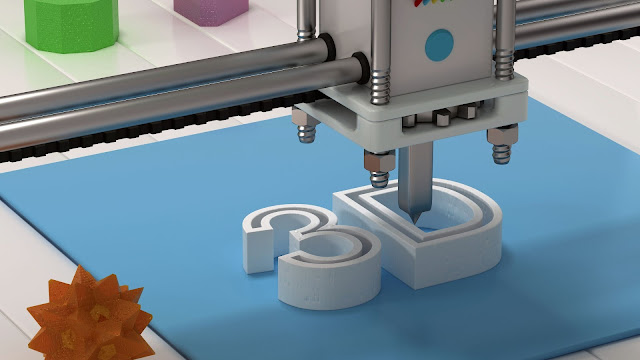
Innovations in Injection Moulding: 3D Printing and Industry Trends Introduction The world of injection moulding is continuously evolving, with technological advancements and innovative solutions driving the industry forward. Among these exciting developments, 3D printing has emerged as a game-changer, revolutionizing the way plastic components are manufactured. In this blog, we will explore the fascinating innovations in injection moulding, with a specific focus on 3D printing, and discuss the latest industry trends that are shaping the future of manufacturing. 1. The Rise of 3D Printing in Injection Moulding Traditional injection moulding has long been the go-to method for mass-producing plastic components with precision and efficiency. However, 3D printing, also known as additive manufacturing, has rapidly gained traction as a complementary and even alternative technique. Unlike conventional moulding, 3D printing builds parts layer by layer from digital models, allowing for complex...